- The HUMLOG Group organises a practitioner workshop on “Private and NGO/GO Collaboration in Emergency Situations and Development” in Jönköping, Sweden, on 24 November.
- The 8th Heinz Nixdorf Symposium has a track on humanitarian logistics. It will be held next year April in Paderborn. Papers can be submitted until 15 November. (H/T to the HUMLOG newsletter).
- ‘Vince Lombardi’ Polak on design for the other 90%. Seems to me that we don’t do too much of that in logistics.
Logistics
At times, the best training you can give people is a game, and that is especially true of logistics.
There are quite a number of counter-intuitive issues in logistics. Probably the most famous one is the Forrester (or whiplash) effect: forward prediction of demand in separate links in the supply chain will often lead to increasing cycles of alternate over- and under-stocks that travel through the chain like the undulations in a cracking whip. In other words: in a situation in which you do not have sufficient information about what happens further down the chain (as is so often the case), trying to look into the future can actually damage reliability and efficiency. Or to put it even more succinctly: don’t try to be smart when your ignorant.
So looking ahead can be bad for you? How is that for being counter-intuitive?
I am not going to explain here why this happens. Instead, I am going to ask you to play a game with a couple of your mates. Each of you is responsible for a link in the production and distribution of beer (hmmmm… how about Mountain Goat?), within a couple of rules – the most important one being that you are not to talk with each other, but only communicate by purchase orders and invoices. Sounds almost like the real world, doesn’t it? I mean, how often do you sit around a table with all supply managers in the full supply chain to see what each of you expects to happen next month?
Setting up the game and organising a play takes a bit of organisation, but luckily there is an online version, graciously run by the Swiss Federal Institute of Technology (who else?). So get a group of mates or colleagues online and play the game – and be astounded by the results. Please do so before reading on after the fold.
So, have you played the game? Then the results as they are explained here by prof. John Sterman should look familiar. Did you expect this to happen? Highly unlikely, unless you had some previous logistics training or have been confronted by the Forrester effect before, either in a game or in real life – or are a natural-born operations research genius, in which case I would love to work with you.
There are two things to notice here. One is that the Forrester effect is only one of a number of very counter-intuitive issues in supply line management; and people who think that you can work large-scale logistics without some understanding of the underlying dynamics and (gasp!) mathematics will find themselves running a supply chain that is either completely unreliable or highly ineffective – probably both. What’s even worse: they would probably not even notice it.
Now please note that I am not saying that we should only use logisticians with an advanced degree in logistics and operations research (although I think having more of these people would be a great thing, for various reasons); but I do maintain that you will need to do a lot of reading on the subject if you ever want to run any supply line that is even marginally larger than your local clinic in a manner that is both effective and efficient. Of course, if you don’t care that you cause regular stock-outs, or that you continuously need to destroy expired drugs that have been lying around in your warehouse for mountain goat’s… ermmm, donkey’s years, than you can forget about all that; but in that case, why are you reading this blog?
The second point to make is that, actually, it is not really necessary to know any of the underlying dynamics and (gasp!) mathematics. Am I contradicting myself here? Not really: you can gain some understanding of the two without having knowledge of it. Just having been confronted by e.g. the Forrester effect in a game is a powerful experience that you will not easily forget, even if you don’t know your regression from your integration; and it will easily teach you the importance of knowing at the start of the supply chain what is happening at its end. Few people who have played the beer game will forget the importance of demand communication throughout the chain, even if they have never heard of kanban or action triggers.
Prof. Sterman’s description of games like these as “flight simulators for management education” is a very good analogy; after all, most flight simulators these days live as games on home computers, even though they started as a safe and cheap way of training pilots. And remember, ‘safe and cheap’ here is ‘safe and cheap as opposed to crashing plane after plane until you get the hang of it’ – which, for some reason, is what we insist on doing in aid logistics.
Now please excuse me; I have a nice, cool glass of beer waiting for me. Mountain Goat, of course.
[Photo credits: Mountain Goat Beer Hightail Ale by Richard Giles; Interior cockpit of a twinjet flight simulator, courtesy of NASA.]

- Family Health International is looking for an associate director, health commodities logistics for Nigeria.
- The Global Fund is looking for a specialist procurement for their HQ in Geneva.
- Concern Worldwide is looking for a logistics manager for Liberia and a logistics and administration coordinator for Congo (DRC).
- UNICEF is looking for “a large number of new colleagues for multiple positions” (how is that for a job description?) for their supply division.
- Medair is looking for a logistics and warehouse manager for Juba (South Sudan).
All you programme managers, country directors, and other people managing aid programmes out there: how often do you integrate logistics planning into your planning from day 1 of your design phase? (And if any of you say: “always”, please let me know when you need an experienced logistics manager – I would just so love to work for you. Not that I would believe you, of course, unless you are a logistician by background yourself – and even then I would be sceptical.)
An old post by Diane Bennett on the Aid Watch blog tells a cautionary tale of what happens when you don’t integrate logistics into your planning. It is a seven-year history of how a lack of logistics planning caused thousands of deaths in remote South Sudan; not because the logistics weren’t thought of, but because they weren’t integrated into the programme from the start.
A medical NGO who wants to support a vaccination will have to take into account how to get the vaccines on the spot – and finding out much later that “… vaccines were available … at a regional distribution center, a $5000 air charter flight away” is too late. If UNICEF and WHO want to ensure vaccination on the spot, they will also need to ensure transportation to it, and possibly refrigeration there. All these should be planned from the start, because this tale clearly demonstrates how taking logistics on at a later stage will only lead to disaster.
But possibly the biggest issue here is that none of the three organisations involved really did their homework. Measles vaccines are fairly heat tolerant. If they would have been transported to the site in a cold box, and then used within a couple of days or even weeks (depending on the ambient temperature), no refrigeration at all would have been necessary. This technique, known as the ‘fast chain’, has been in use for some time and is endorsed by WHO; but apparently nobody managed include this in the planning.
The tale shows only one thing: include logistics and logisticians in your planning from the start, and you will sleep a lot better at night. And don’t we all want that?

Continue Reading 0 comments }Aid and aid work, Logistics, Public health
- EQUIP Liberia is looking for an operations/logistics coordinator for Liberia.
- The International Planned Parenthood Federation is looking for a logistics management advisor for Kenya.
- The IRC is looking for a logistics coordinator for the Central African Republic.
- Save the Children UK is looking for a logistics manager for the DRC.
- UNICEF is looking for a supply chain consultant to help write a new supply manual, and for a supply and logistics manager for Angola (don’t ask me why they post this vacancy a second time on their site).
- The IMC is looking for a logistics coordinator for Cameroon (although that opening is not mentioned on their own site).
- The UNRWA is looking for a procurement and logistics officer and a head of the contractual procurement section, both based in Jordan.
- ACTED are looking for a logistics intern for the DRC.
So it’s a pandemic, now what? Let’s assume you’ve read through Michael’s post on contingency planning and his follow-up ‘the logistics of swine flu aid’ and your organisation has updated their pandemic preparedness plans, or is in the process of doing so now. Did you think of everything?
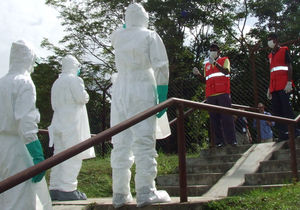
Meeting counterparts. Source: A.Cook
Let’s take another look at your;
- Supply chain
- Staff protection
- Programme operations
Supply chain and border crossings
Contingency planning done at country level with UN PIC and governments suggests an increased role of national military and police in case of a pandemic outbreak when national services and infrastructure will be impacted.
A high level of staff absenteeism (30% or higher) will extend to your suppliers; make sure to include them in your plans. Will your logistics staff and your shipping agent and main transporter be able to handle customs clearance and possible extra measures for quarantine and maintaining security of supplies? Do they know how to handle cold chain & clearance procedures for medicines & vaccines, which may be needed during a pandemic?
Staff protection
You’ve considered protective equipment for your staff who will be in contact with influenza patients (either at work or at home) and may have purchased particulate face masks, gloves and hand washing gel, maybe even Tyvek protection suits if you’re with a medical organisation.
Did you consider training for protective measures? A pandemic logistics simulation training P2LX in Nov.2008, found that a major part of using protective equipment is learning how to assess the level of risk and deciding when to use it. And: You learn by doing it, not by reading about it. Secondly, the protection of this type of equipment is only effective when used properly.
Programme operations
You went through the four steps as recommended in this earlier post ; prioritise your logistics, sensitivity analysis, contingency planning and communication.
Your contingency planning answered the important question: How will your programme operations adapt to a national pandemic situation, with significantly less human resources and an increased strain on the supply chain?
Does your pandemic preparedness plan extend to your offices at field level? And does it include your local implementing partners? If not, perhaps now is the time to sit down with your partners at field level to discuss their role and activities.
Take note that staff protection will also affect them. How will they deal with it when your staff has all the protective gear and they don’t? Things could get ugly.
In case you are with a medical organisation, did you consider the additional requirements or shift of focus of your programme if you’re suddenly confronted with a surge in influenza patients and deteriorating local healthcare services?
Conclusion
Now that H1N1 has spread globally and a pandemic has been officially declared a possibility is that we will continue to see a gradual increase in cases, until a larger local outbreak happens in a particular region or perhaps your country.
To maintain the key activities of your programme in the field during an outbreak, the basic principle of the supply chain still applies: the chain is only as strong as its weakest link. Your programme operations will only continue successfully if you have looked beyond your own organisation and included suppliers and local implementing partners in your planning, communication and training.
(Guestpost by Jurgen Hulst, @NFIguy)
{
- Samaritan’s Purse is looking for a country logistics manager for North Sudan.
- Merlin is looking for logisticians in Manguredjipa/Butembo and North Maniema, both in the DRC.
‘Chasing’ Carly writes about how a distribution went rather wrong, under the title Crowd Control. So how should you organise a distribution?
- Make sure that the recipients know in advance when and how the distribution will be organised. In Carly’s case, probably the right time to do so would have been when the coupons were handed out, the day before.
- Make sure that the goods are there when promised, and make sure you have enough. Nothing will incite a riot as handily as handing out goodies to the first half of the crowd and then tell the other half they will have to go back home empty-handed.
- Make sure your distribution area is well prepared. As Carly observes, nobody likes to stand in the sun (or rain, or driving wind) for long periods of time, so make sure there are shelters; use rope and posts to demarcate corridors for lines; prepare signs for the various queues; make sure that you have communication equipment (a.k.a. a megaphone or bullroarer); ensure water, sanitation, and where appropriate, food are available; etcetera, etcetera. If you start thinking about this on the day itself, you are definitely too late.
- Make sure that your registration system is prepared. I will write more about this at some time in the future (thank you, Rob Stephenson, for giving me some serious food for thought on the subject).
- Make sure that you have crowd control systems in place. Have ‘crowd controllers’ in situ several hours before the distribution starts. Ensure that they are clearly recognisable. Have authority figures from the community (elders, church leaders, whatever works in the context you are in) assist them by bolstering their clout and by defusing possible conflicts. Make sure that everybody knows what to do when things get really ugly (basically: run).
- Make sure that you have logistics back-up capacity. Have one or more people with some logistics experience at the ready who are not directly involved in the distribution itself, and who can jump in when logistics (for whatever reason) breaks down. Ensure that they have sufficient extra materials (rope, plastic sheeting, water, duct tape, spare megaphone, etcetera, etcetera) to be effective.
And a bonus step: don’t call in the cavalry unless lives are in danger. In most aid contexts, it is a sure-fire way to lose cooperation.
A little exercise for the reader: why is the title of Carly’s post incorrect? (I suspect it is on purpose – a more descriptive title would probably draw far fewer readers.)
{The regular logistics job postings on A Humourless Lot always draw a predictable amount of steady attention. Obviously, none of them gets as much attention as, say, the post on pandemic contingency planning, but if you add them all up, they are responsible for a large chunk of traffic on the site. I think it is safe to say that there are quite a number of people out there looking for a (new) job in logistics for health and aid.
I think it is also clear that there are quite a number of organisations that are desperately short of qualified, experienced staff. So why on earth do they make it so difficult for people to find their vacancies?
Some of the worst practices I have seen over the last couple of months:
- Posting vacancies late (less than a week before closing). In one case I even saw a vacancy being posted on ReliefWeb after the closing date[1] .
- Posting incomplete vacancies: no submission details, no person to contact for further information, nothing about the further process, incomplete or missing requirements or even details of job content… the list is endless.
- Spelling mistakes that make finding jobs a lot more difficult. One ‘interesting’ example was how Goal Ireland managed to consistently spell ‘logistics’ as ‘logisitics’ in the titles and descriptions of a whole slew of their vacancy postings – so if anybody had searched for ‘logistics’ vacancies on their site, they would never have found them.
- Posting vacancies that are not really vacancies. We all know them: those job openings for which the ideal candidate is actually already selected, and are only posted for form’s (or internal regulations’) sake. Don’t do it: the word will go around, and your next opening will not get candidates from the people in the know, who will all have heard about your despicable behaviour, but from the poor newbies who haven’t heard – exactly the people who you want to apply for you high-level logistics management position, right?
- Only posting on your own site. You think that everybody has the opportunity to go and make regular visits to every single site? Be smart: post your job openings on the main inter-agency sites.
So next time when you complain about the lack of qualified candidates for your logistics positions, just first look at your own job publication practices
Footnote
Back to post [1] That particular posting was later removed. A pity, I would have loved to name and shame.
{- The Global Fund is looking for a senior technical officer – global health supply and a senior advisor: supply chain management and strategic support.
- The UNDP is looking for a procurement specialist for Afghanistan and a procurement advisor for their HQ.